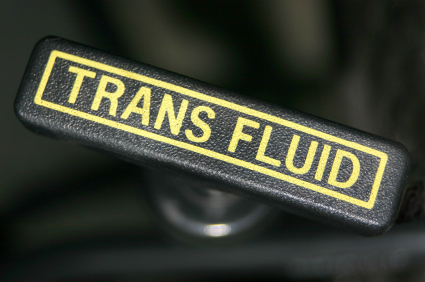
Transmissions For Sale
The third way to do this will work on practically any car with a transmission dipstick tube. It requires some brazing or light welding. It has been used on some of the old AMC or Ramblers that outsourced their transmissions to Borg Warner in the 1950,s and ’60’s and even some more modern cars. It is a very effective method of venting a transmission and being able to run a hose to a higher point on the vehicle.
What we want to do is buy a 1 foot long piece of 5/16 of an inch outer diameter metal brake tubing. The point is to drill a 5/16 ” hole in the dipstick about 2/3″ from the bottom. Or, close to the top of the dipstick. Cut one of the flared ends of of the piece of brake line. You will need to silver solder the 5/16” brake line or braze the brake line into the hole in the dipstick. Insert the brake-line about 1” into the dipstick, leaving most of the brake-line exposed. Silver solder or braze the metal brake-line to the metal dipstick all the way around. After the piece of metal is cooled down, cut the long piece of brake-line sticking out of the dipstick tube to about 4” long. After the dipstick is reinstalled with a new dipstick o-ring, attach a piece of 5/16” inner diameter transmission rubber hose to the piece of brake-line extending out of the dipstick and run it to the top of the firewall.
For all practical purposes this is a universal method of venting a transmission, automatic or not. I have personally done it many times at my transmission shop on jobs where we would install an overdrive transmission in place of an outdated 3 speed transmission. Sometimes we did custom hot-rod transmission work.
No matter, if you don’t have proper ventilation to your automatic transmission, it will eventually find other places to vent ATF and spring a leak.
Find out how to vent your transmission in other ways in our blog or simply enjoy more cost saving articles for your car. Our specialty is selling replacement transmissions. Got a transmission problem or question? Call GotTransmissions.com @ 866-320-1182.